Steel Bar Grinding Solution
Based in Clinton Township, MI, Excel Industrial Electronics, Inc. stands as a leading industrial distributor, system integrator, and Yaskawa authorized service provider. This firm, reputed for customized, cost-effective drive solutions, adeptly applied a Yaskawa U1000 Industrial Matrix drive to resolve a steel bar grinding issue experienced by a machine builder in Detroit.
- Industrije
- Metalworking
- Aplikacije
- Material Handling
- Grinding | Polishing
- Stranka
- Excel Industrial Electronics Inc.
- Centerless Grinder Repair
- Izdelki
- CIMR-UC - U1000 Serija
Application Challenge
Centerless Grinder Repair (CGR), a company located in Roseville, MI, required a method to enhance and optimize the performance of its centerless grinding machines that catered to the steel bar market. The existing machines incorporated standard variable frequency drives coupled with dynamic brake resistors. These systems functioned satisfactorily with light stock removal (ranging from .008/in. to .012/in.) and shorter steel bar stock lengths. However, issues arose when loading longer steel bar stock lengths with a higher stock removal requirement. In such situations, excessive heat accumulation in the dynamic brake resistor. With an ineffective resistor, the drive would immediately stop the motor due to an overvoltage (ov) fault. This resulted in considerable downtime while waiting for the resistor to cool down. Increases to the steel bar stock's weight, length, and cut increased the machine's downtime due to frequent ov faults.
The project’s primary objectives included enabling the machine builder to feed steel bar stock without restrictions on weight, length, and grinder cut, thereby improving customer productivity.
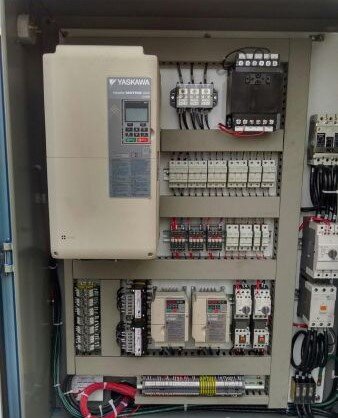
The Solution
Excel Industrial Electronics introduced the U1000 Matrix drive to CGR to accomplish the primary goals, save energy, and eliminate moving parts and peripheral components. Differing from conventional drives, the U1000 has no DC link circuit with diode and main capacitor, resulting in higher efficiency.
The centerless grinding machine is operating with a 10 HP, 460 V U1000 Matrix drive and a 5 HP induction gear motor (10:1 ratio). By implementing the U1000, the machine can increase throughput due to the drive’s ability to immediately redirect energy back onto the line. This allowed continuous drive operation during periods of excessive demand.1 ratio). By implementing the U1000, the machine can increase throughput due to the drive’s ability to immediately redirect energy back onto the line. This allowed continuous drive operation during periods of excessive demand.
(Source: Yaskawa America, Inc.)
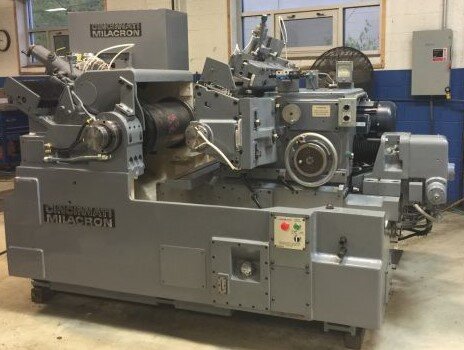
Results
The full regeneration capability now allows the machine to handle longer bar stock lengths, heavier steel bar weights and deeper cuts (> .024/in) while returning the regenerative energy to the utility company to save energy rather than being discarded as heat.
CGR has successfully provided its customers with machines that are performing optimally and has allowed its customers to increase production, save energy, and eliminate costly components.
(Source: Yaskawa America, Inc.)