Start up made easy - Flexible servodrive for butter packing plant
Whether it is a new product or a retrofit, starting up a machine for the first time is always an exciting moment. The same feeling arises when integrating drive technology. This makes it all the more satisfying when start up of the drive on site goes so smoothly that even experienced mechanical engineers are amazed. The following two applications demonstrate how easily this can be achieved using servodrives.
WAL Mess- und Regelsysteme GmbH of Oldenburg, northern Germany, develops and produces measurement systems and controllers for industrial use. The main purpose of these systems is to measure and control physical variables. The company also manufactures custom solutions for the food industry. One such solution is a fully automated filling and packaging plant for butter, vegetable fats and other food pastes (Image 1). Yaskawa servodrives are used in both the butter packaging plant and an additional module connected to it – a carton erector (Image 2).
Reliable processing
The fully automated butter filling and packaging plant fills and packages 25 kg units of butter. The plant guides an empty carton to the filling position, lines the inside of it with foil and then fills it. This is done with the aid of a drive, which enables the plant to pull the foil off a roll (Image 3), cut it to the required length and lay it around the filler head. The filler head is then inserted into the carton together with the foil. When the filler pipe pumps the butter into the filler head, the head thus “swims” up to the top of the package on the surface of the butter. Durability and hygiene were key considerations when it came to designing the machine: The interior sections needed to be easy to clean, and fully automated CIP (Cleaning in Place) was a must for every component that comes into contact with the product, as well as the inside and outside of the filler head. The modular design of the plant keeps start up times short and makes it easy to expand.
The motorized foil supply unit unrolls evenly without running on. Together with the exact foil lengths, this ensures that packaging is carried out reliably. In the past, the foil was pulled off using a stepper motor. Without regular maintenance, this motor often broke down. The difficulty was compounded by the design of the stepper motor, which prevented it from reaching its maximum torque unless at a standstill and caused the torque to decrease as the unit built up speed. The act of pulling on the foil roll increasingly required a dynamic response that the stepper motor was unable to provide. A servodrive was required (Image 4). Mathias Willner (Image 5), Technical Director at WAL Mess- und Regelsysteme GmbH, explains: “We sell our plants not just in Europe, but in the USA as well. Because of this, one of the key requirements for our new servodrive was that it had to support both Profinet and EtherNet/IP as communication media. We found a good solution in the Sigma7 (see technology box) from Yaskawa.” Both the European and the American models of the butter filling plant are fitted with the same AC servo motor. The only change is the servo amplifier, which is chosen to match the required bus interface in each case. The new plant also provides another improvement that has delighted Mr. Willner: “In some countries, we were having problems with imprecise power supply voltages. That was a real challenge for the stepper motor, but the servodrives keep running reliably even in the face of fluctuating power supply voltage.”
Well equipped
As a companion module to its butter filling plant, the northern German company also provides a carton erector. This module runs a fully automated process that takes up to 12 folded cartons per minute out of a magazine, seals the folded base flap with adhesive tape and transfers the carton to the filling station. This plant has been developed from scratch, rather than as a retrofit. Due to the high number of cycles required, servodrives were the obvious solution for this task right from the start. “We use another two Sigma-7 drive in this plant module,” Mr. Willner reports. “Since we were so impressed with both the Sigma-7 servodrive retrofit on our butter filling plant and how easy it was to work with the Yaskawa staff, we installed the same drive types here.” This machine gives the Sigma-7 another opportunity to show off the advantages it offers (Image 6): The servo amplifier is very much the “brain” of the system (Image 7). Functions such as the tuningless option, vibration suppression, the resonant filter, ripple compensation, and many more besides, are available regardless of the higher-level control.
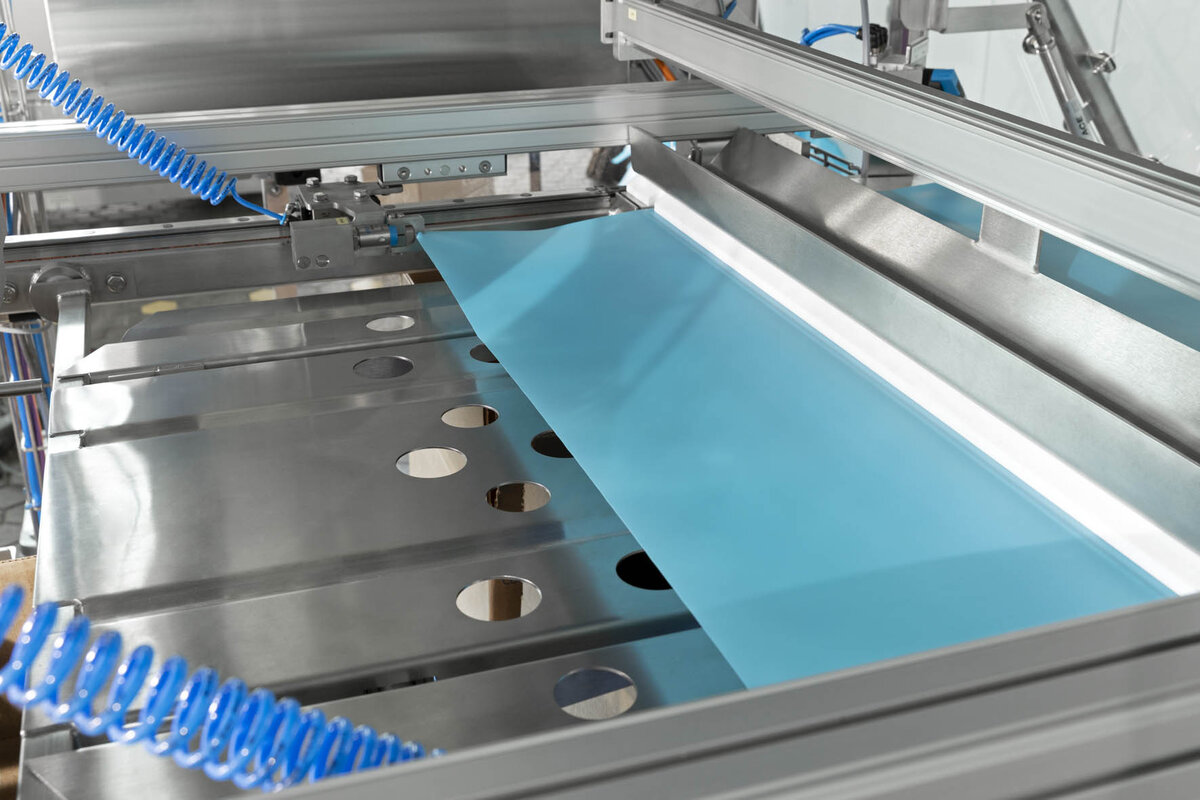
Fast setup
Ultimately, how good a drive really is also depends on how easy it is to start up. Yaskawa has developed a tuningless function for this purpose. When this function is used, the servo amplifier continuously and independently adapts its control parameters to the situation at hand. This allows the drive to be put into operation immediately without the need for complex parameterization or special knowledge of control equipment. This function is entirely sufficient for most applications. But of course, additional tuning functions are also available for highly demanding applications. Mr. Willner was certainly impressed by the fast start up: “We’d made all the preparations: installing adapters to set up the mechanical interfaces for the motor and setting up the necessary control protocols, of course. The process of integrating the drives in the butter filling plant itself was completed in half a day. The Yaskawa staff provided outstanding help for both applications.” Integrating the drives in the carton erector also took less than one working day.
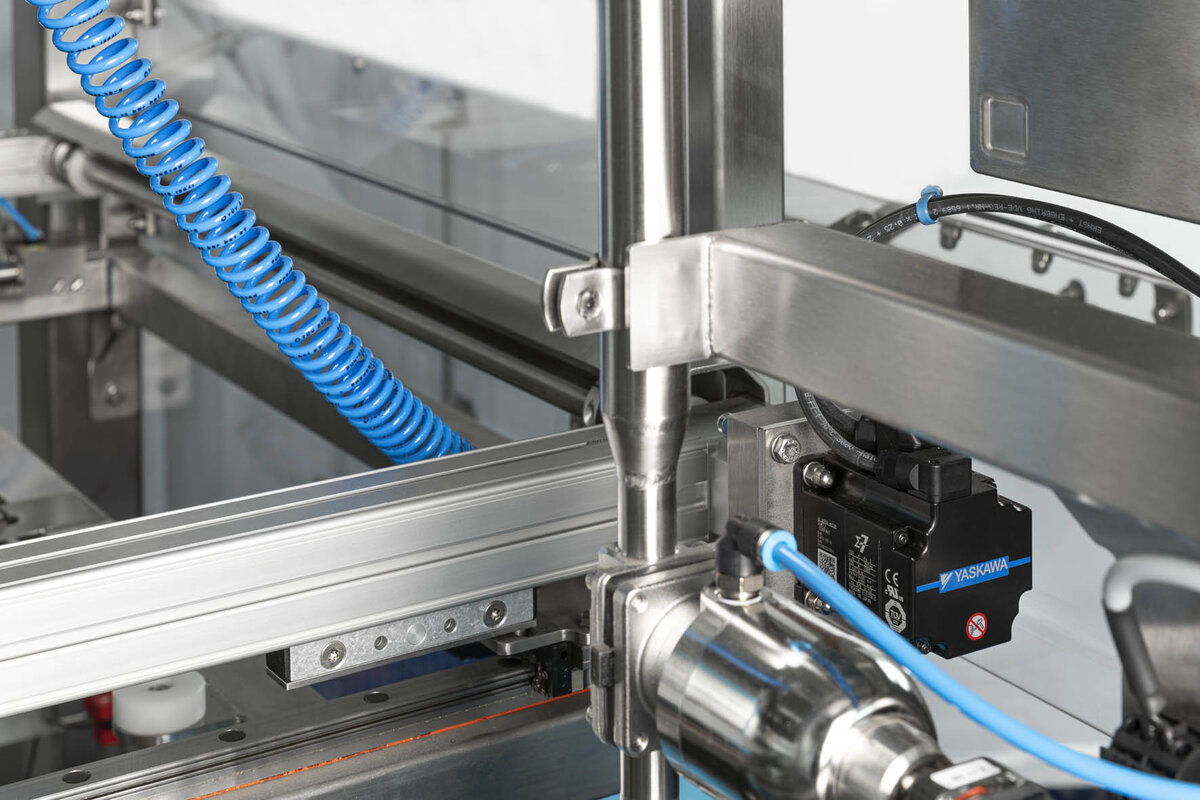
Technology box: Sigma-7 servodrive
During development of the servodrives in the Sigma-7 series, the focus was on three main objectives: rapid start up, high production output and maximum operational reliability. The responsive servo motors cover outputs from 50 W to 15 kW at supply voltages of 200 and 400 V, boast extremely compact dimensions and are very quiet when running. The series includes narrow single- and double-axis amplifier modules for 200 V or 400 V in a space-saving design. These can be lined up seamlessly in the control cabinet and can easily be daisy chained if required. This reduces the complexity of the installation process, while the efficient utilization of space enables very high power density for control cabinets. There is also a further advantage in terms of space: At ambient temperatures of -5°C to +55°C, no additional cooling is required. The servos boast an impressively high resolution (integrated 24 absolute encoder), high dynamics as well as functions such as vibration suppression, jump frequency and a tuningless function for simple start up.
As an alternative to the servomotors, linear motors can also be operated on the same amplifiers, while torque motors can also be operated with the 200 V version,. Typical areas of application for the compact AC servo systems include packaging machines, semiconductor manufacturing plants, woodworking plants and digital printing machines.
Image info:
Image 1: Fully automated filling and packaging plant for butter, vegetable fats and other food pastes
Image 2: Carton erector
Image 3: Cutting the foil to length
Image 4: Servodrive for cutting the foil to length
Image 5: Mathias Willner, Technical Director at WAL Mess- und Regelsysteme GmbH: “We were very impressed with both the Sigma-7 series servodrives and how easy the Yaskawa staff were to work with.”
Image 6: Sigma-7 in the carton erector
Image 7: The servo package is the brains of the drive. Thanks to their space-saving design, the amplifier modules can be lined up seamlessly in the control cabinet and can easily be daisy chained if required.